What Is Backflow Testing And Why Is It Necessary?
July 6th 2022
On the most basic level, backflow is caused when the pressure in a water system malfunctions, causing potentially contaminated water and waste to flow in the reverse direction.
Backflow testing is the procedure by which backflow prevention devices (BPDs) are checked to ensure that they are working properly. Because BPDs prevent contaminants from flowing in the reverse direction through private water systems, it is critical that they remain in good working order.
The purpose of a BPD is to prevent potentially dangerous contaminants from getting into your drinking water. This includes things like pesticides or industrial chemicals entering your home through hose bibb systems, sprinkler systems, and irrigation equipment.
This can be hazardous to both health and safety. Anything that is potentially contaminated should not be going into a building's water supply. Therefore, it is vital that backflow prevention devices are tested and maintained regularly to ensure they're working properly.
When there is a discrepancy or failure in the system, a cross-connection is created between the building water supply and drain, waste, and vent systems. One of our certified technicians will conduct 3 separate tests to determine what the problem might be if this occurs:
Backflow testing is the procedure by which backflow prevention devices (BPDs) are checked to ensure that they are working properly. Because BPDs prevent contaminants from flowing in the reverse direction through private water systems, it is critical that they remain in good working order.
The purpose of a BPD is to prevent potentially dangerous contaminants from getting into your drinking water. This includes things like pesticides or industrial chemicals entering your home through hose bibb systems, sprinkler systems, and irrigation equipment.
This can be hazardous to both health and safety. Anything that is potentially contaminated should not be going into a building's water supply. Therefore, it is vital that backflow prevention devices are tested and maintained regularly to ensure they're working properly.
Are You At Risk Of Backflow Contamination?
Backflow can occur when there is back pressure that creates siphonage and the water runs backward against the normal flow. If negative pressure is created, then back-siphonage produces reverse flow. It occurs when a potable water supply is fed at a higher pressure than a non-potable source. This increases the likelihood of cross connection.How Are Cross Connections Tested?
A backflow prevention device will prevent cross-connection between the potable water supply system and the non-potable water supply system. The most common purpose is to prevent the cross-connection of a building's contaminated public water supply with its clean, private water system.When there is a discrepancy or failure in the system, a cross-connection is created between the building water supply and drain, waste, and vent systems. One of our certified technicians will conduct 3 separate tests to determine what the problem might be if this occurs:
- Our technician will need to take note of the backflow static pressure. The outside diameter of piping may also be measured with a pipe gauge. The goal is to make sure that more than 3% of the pressure is remaining after it passes through the Double Check Valve Assembly to ensure it is functioning correctly.
- Another item to observe during backflow testing is excessive leakage at Check Valve 1. This test is performed by increasing the pressure in the First Shut Off, then releasing the pressure without opening up the First Shut Off to allow flow through Check Valve 1. If Check Valve 1 leaks excessive amounts of water after releasing the pressure, it does not comply.
- To test the shut-off control of Check Valve 2, our technician will set up the testing equipment as previously explained, however, this time attaching it to Check Valve 2. Check Valve 2 is now in a position where it must reverse the water flow if Check Valve 1 fails and if required must also stop the flow of water through itself. This action is simulating what would happen if Check Valve 1 should fail or become stuck open.
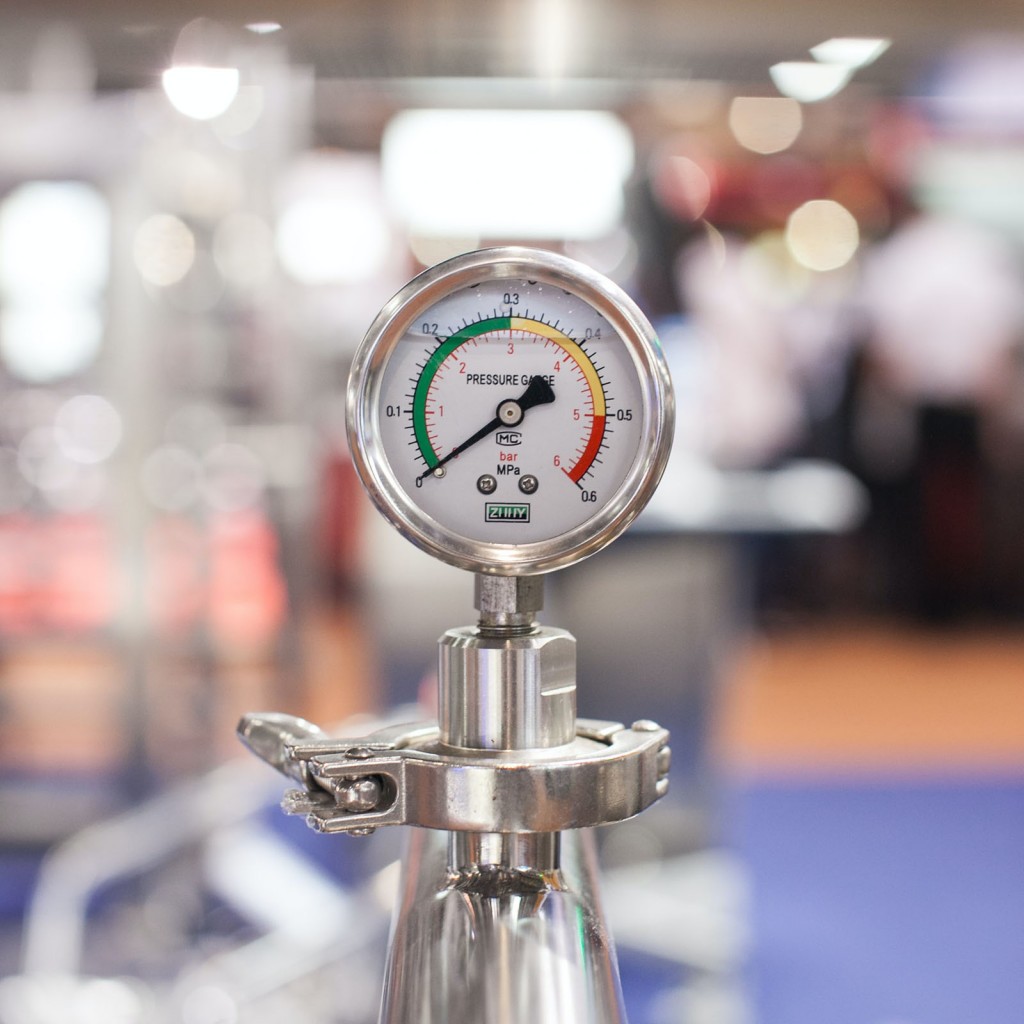
Click to close